The Hidden Cost of Underperforming Factories on Your Bottom Line




Based on 40M reviews




Based on 40M reviews




Based on 40M reviews
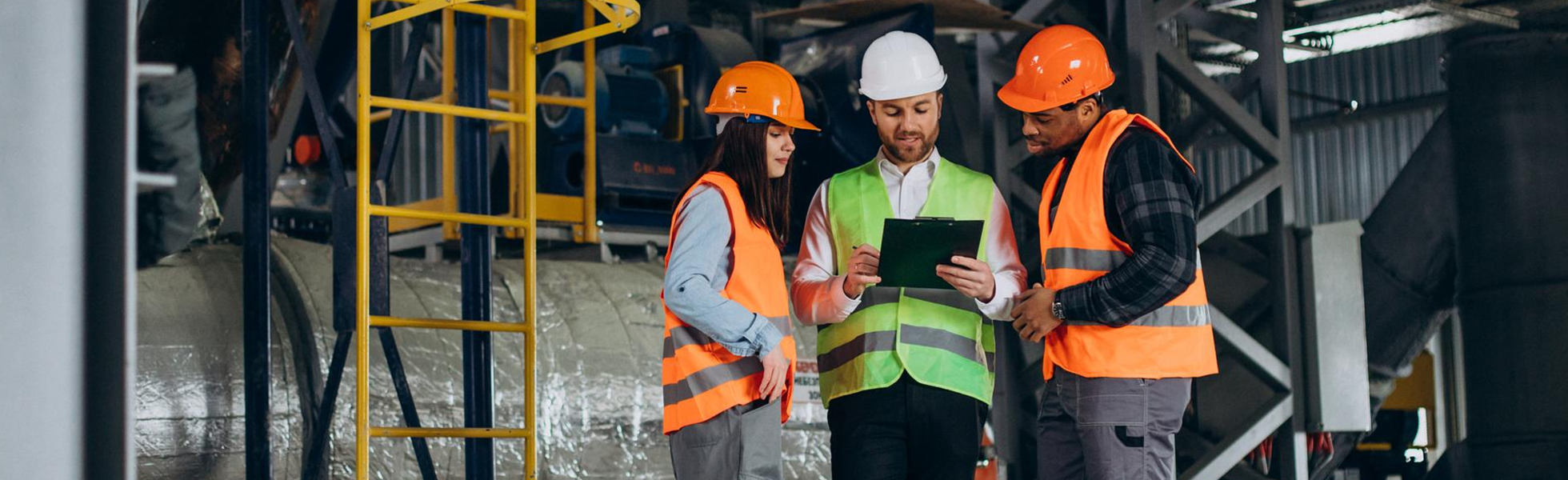
Manufacturing is a highly competitive industry, and managing multiple factory sites comes with real challenges. Without a clear view of what’s happening across all your locations, it’s easy to miss issues that quietly impact your bottom line. Let’s explore how underperforming factories affect profitability and how smart Financial Management tools in a modern ERP system can help you identify and solve problems proactively.
What Does ‘Underperformance’ Look Like?
Underperformance in a factory isn’t always easy to see, at least not until it starts showing up in your profit margins. The signs are there, though. Frequent downtime, low output, rising defect rates, and recurring safety issues can all indicate deeper underlying problems. One of the most common causes behind these issues is a bottleneck. In multi-site operations, long-term bottlenecks are easy to miss. If left unchecked, they cause delays, drive up costs, and reduce performance, all of which directly impact profitability.
How Factory Inefficiencies Affect Your Bottom Line
In the automotive industry, an hour of lost productivity can cost up to $2.3 million in revenue. And downtime is just one type of factory inefficiency. Equipment failures,
manual processes, supply chain disruptions, and even minor communication delays all erode your profits.
A recent Siemens survey found that inefficiency costs are rising rapidly, particularly in the heavy industry sector; they’ve increased fourfold over the past five to six years. In the oil and gas sector, losses tend to rise with oil prices, making downtime even more costly.
The financial hit from inefficiency doesn’t stop at lost sales. Even when production stalls, payroll keeps running, emergency repairs accumulate unexpected costs, and missing deadlines can result in penalties or strained client relationships.
These hidden expenses are rising much faster than inflation, leading to significant revenue loss in manufacturing. Between 2019 and 2023, inflation rose by about 19%, but inefficiency costs increased by 113% in automotive manufacturing and an astonishing 319% in heavy industry. Smaller factories feel the pressure, too — an hour of lost productivity can cost up to $150,000.
Why Many Multi-Site Manufacturing Companies Miss the Signs of Underperformance
With disparate legacy systems in place, early signs of underperformance often go unnoticed. These seemingly minor issues can quietly escalate into major problems.
Here are six main reasons small issues slowly grow into major problems:
1. Real-Time Visibility Blocked: 74% of Manufacturers Still Use Legacy Systems
When each manufacturing site uses its own system, critical information ends up scattered. This makes it nearly impossible to get a complete and accurate
picture of what’s happening across all the locations.
2. Inconsistent Processes
Different sites often follow different methods. This makes it harder to see what’s working, what isn’t, and where improvements are needed.
3. Delayed Reporting
By the time manual reports reach decision-makers, the situation has already escalated, and it’s too late to respond effectively
4. Misleading Metrics
Without unified data, performance indicators can be unreliable or even misleading.
5. Limited Collaboration
When sites operate in silos, they miss opportunities to share knowledge and solve common problems faster.
6. Lack of Root Cause Insights
Fragmented data keeps you focused on symptoms instead of addressing the root cause.
How do most manufacturing companies try to solve these issues? Many companies add more resources, which doesn’t solve the problem and only drains their budget.
The solution lies in:
- Leadership commitment: Make investing in a multi-site ERP system a priority to connect all sites.
- Standardized processes: Set company-wide standards to ensure operations and performance are uniform across locations.
- Cross-site collaboration: Share insights and successes between sites to boost overall performance.
How Modern ERP Systems Can Address These Challenges
Modern financial and inventory management tools within systems like achieve-ERP are built to keep everything running at maximum efficiency, allowing you focus on growth
instead of constantly tackling issues.
Here’s why investing in an advanced financial and inventory management system is the smartest move you can make:
1. Cut Inventory Costs by Up to 22%
With an inventory management system in place, companies cut inventory costs by an average of 11%, with top performers saving up to 22%. Depending on company size, ERP-driven inventory savings can range from $100K to over $600K annually.
2. Reduce Operating Costs and Processing Time
3. Get Smart with Data
4. Keep Things Consistent Across All Sites
Using a single ERP system across multiple locations means standardized processes everywhere. When everyone is on the same page, it saves time, reduces errors, and helps maintain consistent quality.
Why Should You Invest in ERP Systems?
Because the long-term value often outweighs the cost. Mid-sized companies typically invest 3% to 5% of their annual revenue in ERP systems, while larger businesses spend around 2% to 3% — a relatively small portion for the efficiency and control ERP delivers. Here’s why it makes sense to invest in a comprehensive ERP for manufacturing:
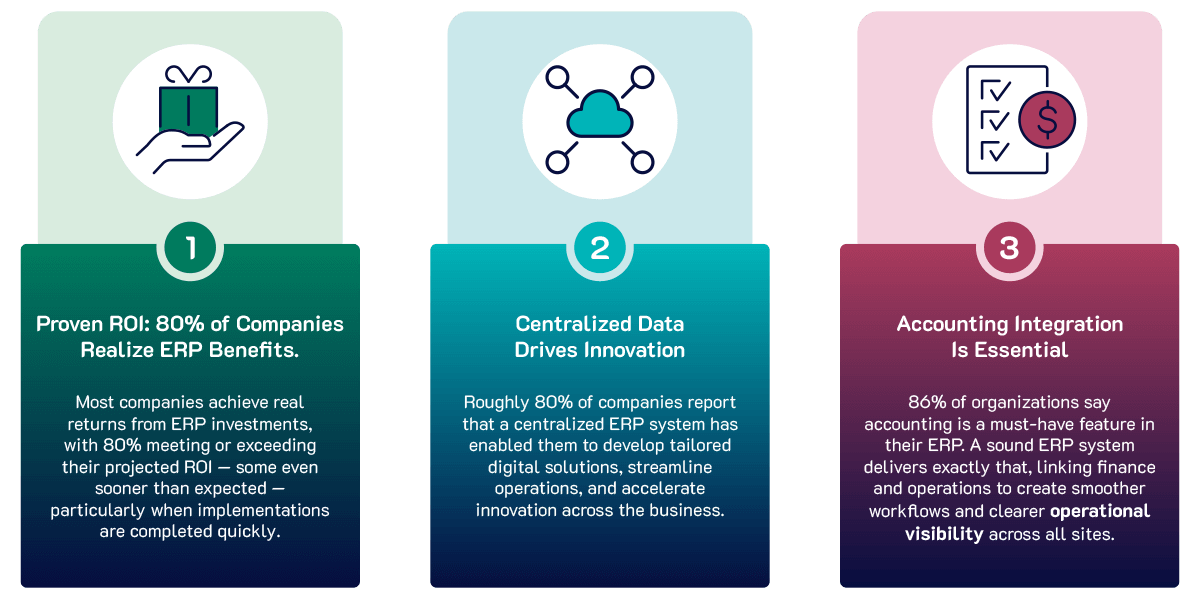
Final Thoughts
From cutting costs to boosting collaboration and agility, financial management tools in a modern ERP help you manage inefficiencies and stay competitive in an increasingly
challenging and ever-evolving market.
For multi-site manufacturers, an ERP system like achieve-ERP offers all these benefits and more, with tools to manage not only your finances and inventory but also your
workforce and assets.
Want to dive deeper?
Frequently Asked Questions
How can a modern ERP system help reduce production costs?
A modern ERP system connects your manufacturing sites by centralizing data and automating tasks. It reduces errors, improves collaboration, and boosts efficiency
while cutting costs and delays.
What are the biggest signs of underperformance in multi-site manufacturing?
Uneven output, equipment breakdowns, rising inventory costs, and late deliveries ares ome of the telltale signs that your manufacturing sites aren’t running smoothly.
Is implementing an ERP system complicated and costly for multi-site manufacturers?
Implementing an ERP system requires planning and investment, but with the right provider, the return on investment justifies the expenditure